AQUAL TO16 Performance Level: Meets IS: 335-1993 Standards
AQUAL TO16 is a high-performance electrical insulating oil specifically formulated for use in electrical systems, meeting the rigorous requirements of the IS: 335-1993 standard. This oil is designed to provide reliable insulation and efficient heat transfer in transformers, switchgear, and other high-voltage equipment, making it an essential component for maintaining the safety, efficiency, and longevity of these systems.
The oil serves as a dual-purpose fluid: it acts as an insulating medium, preventing electrical discharges and short circuits by ensuring effective separation between live parts. Simultaneously, it functions as a heat transfer medium, dissipating the excess heat generated by electrical components and protecting them from thermal degradation.
AQUAL TO16 is particularly suited for environments where normal oxidation resistance is required, ensuring stable performance over extended periods of use. Transformer oil properties, help to maintain the electrical integrity of transformers and other critical equipment under high voltage stress. Moreover, its superior thermal conductivity allows for efficient cooling, preventing overheating and reducing the risk of equipment failure.
By complying with the IS: 335-1993 standard, AQUAL TO16 guarantees optimal performance and safety, making it an ideal choice for a wide range of electrical insulation applications, including power transformers, distribution transformers, and high-voltage circuit breakers.
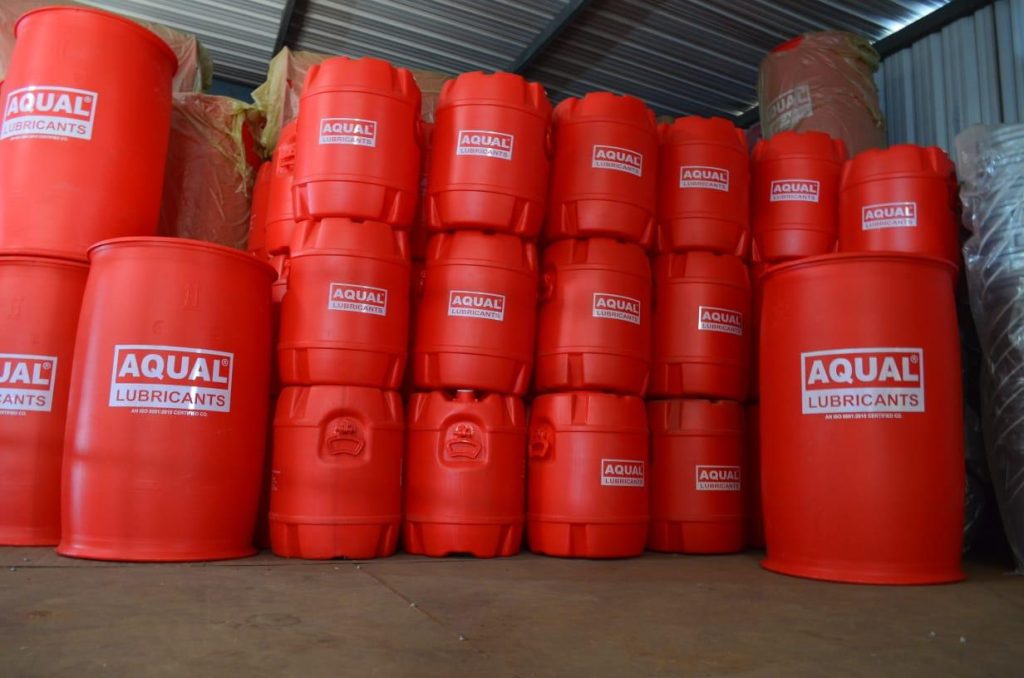
AQUAL TO16
Performance Level: Meets IS: 335-1993
AQUAL TO16 is an electrical insulating oil suitable for use as an insulating and heat transfer media in electrical systems where normal oxidation resistance is required.
Technical Specifications:
Characteristics | Result |
---|---|
Appearance | Bright & Clear |
Density @29.5ºC | 0.832 |
Flash Point ºC | 150ºC |
Pour Point ºC | -15ºC |
Viscosity @27ºC | 20-24 |
Copper Strip Corrosion Test | Non-corrosive |
Functions of Transformer Oil
Insulation:
Transformer oil plays a critical role in insulating the transformer’s internal components. It surrounds the transformer windings, preventing electrical arcing and ensuring that different parts of the transformer remain electrically isolated from each other. Without this insulation, high-voltage electrical fields could cause breakdowns, leading to severe damage or failure of the transformer. Transformer oil must maintain a high dielectric strength to ensure it can withstand electric stresses without breaking down.
Cooling:
Transformers generate significant heat during operation due to the resistance in windings and magnetic losses in the core. The transformer oil circulates around the windings, absorbing heat and transferring it to radiators or cooling systems. The oil’s ability to effectively conduct heat is crucial to prevent overheating and maintain stable transformer operation. In large power transformers, the oil may be actively pumped through external heat exchangers to increase cooling efficiency. Proper cooling helps maintain optimal performance and extends the life of the transformer.
Arc Suppression:
In case of electrical faults or high-voltage breakdowns, transformer oil plays a critical role in suppressing electric arcs. Arcing can cause severe damage, leading to transformer failure or even fire. The oil, with its high dielectric properties, ensures that the electric arc is extinguished quickly by resisting ionization. This feature protects the transformer and surrounding systems from catastrophic failures and reduces the risk of accidents.
Moisture Absorption:
Moisture is one of the primary enemies of transformer performance, as it reduces the dielectric strength of insulation materials and accelerates their degradation. Transformer oil absorbs moisture from solid insulation materials like cellulose-based papers, helping to preserve their insulation properties. By doing so, it prevents the formation of water pockets, which could cause electrical breakdowns or corona discharge within the transformer. The oil’s ability to manage moisture ensures long-term insulation reliability and safety.
Protection Against Corrosion:
Metal parts inside transformers are prone to oxidation and corrosion, especially in high-temperature environments. Transformer oil forms a protective layer on these metallic components, preventing direct contact with oxygen and other corrosive elements. This protective barrier reduces oxidation, which in turn helps avoid rust formation and ensures smooth operation of internal mechanical parts over extended periods. The oil’s role in corrosion prevention is critical in maintaining the integrity and lifespan of the transformer.
Key Properties of Transformer Oil
Dielectric Strength:
The dielectric strength of transformer oil refers to its ability to withstand high electrical stresses without breaking down. A high dielectric strength ensures that the oil can resist electrical discharges, preventing short circuits or electrical faults within the transformer. Fresh transformer oil typically has a dielectric strength of 30-50 kV (kilovolts), and it is periodically tested during maintenance to ensure that it continues to meet this standard. Any significant drop in dielectric strength could indicate the presence of contaminants, moisture, or oil degradation, which would necessitate immediate action.
Thermal Conductivity:
The efficiency of a transformer largely depends on its ability to dissipate heat. Transformer oil, due to its excellent thermal conductivity, absorbs heat generated by the transformer’s core and windings and transfers it to external cooling systems. By reducing the core temperature, transformer oil temperature range prevents the breakdown of insulation materials and avoids thermal stresses that could lead to transformer malfunction. The thermal conductivity of the oil must remain stable even under high-load conditions to ensure that the transformer operates safely without overheating.
Low Viscosity:
The viscosity of transformer oil is a critical factor in determining its flow characteristics. Low-viscosity oil flows more easily through the cooling channels of the transformer, ensuring uniform heat distribution and effective cooling. If the oil becomes too viscous, especially at low temperatures, it could impede the cooling process, leading to localized overheating. The oil’s viscosity is also important for oil circulation in natural convection-based cooling systems, where no external pumps are used.
Moisture Tolerance:
Transformer oil has a natural affinity to absorb moisture from the atmosphere and from the insulation materials inside the transformer. It must have the ability to tolerate small amounts of moisture without compromising its insulating and dielectric properties. Excessive moisture can severely reduce the oil’s dielectric strength, increasing the risk of arcing or electrical breakdowns. Transformer oil is regularly tested for moisture content, and dehumidification or oil replacement may be necessary if moisture levels exceed safe thresholds.
Oxidation Stability:
Over time, transformer oil is exposed to oxygen and elevated temperatures, which can lead to oxidation. Oxidation produces sludge, acids, and other byproducts that can adversely affect the oil’s insulating and cooling properties. High oxidation stability ensures that the oil remains stable over long periods without significant degradation. Oils with high oxidation stability help avoid sludge buildup, which could block cooling channels, and they reduce the formation of corrosive acids that could damage internal components.
Chemical Stability:
Flash Point:
The flash point of transformer oil is the temperature at which the oil vapors can ignite in air. A high flash point is essential to minimize the risk of fire under normal operating conditions. Transformer oils typically have flash points above 140°C, ensuring that the oil does not vaporize or ignite under high temperatures. Regular monitoring of the flash point helps ensure that the oil remains safe for use, particularly in high-voltage or high-load applications.
Pour Point:
The pour point is the lowest temperature at which the oil remains fluid. Transformer oils with a low pour point can function effectively in cold climates, ensuring that the oil continues to circulate even at low ambient temperatures. If the pour point is too high, the oil may solidify or become too viscous, leading to poor heat dissipation and increased risk of transformer failure. Maintaining an appropriate pour point is essential for transformers operating in cold weather regions.
Neutralization Number (Acidity):
The neutralization number, also known as the acidity number, indicates the presence of acidic compounds in transformer oil. Acids form as a result of oil oxidation, and high acidity levels can cause corrosion of metallic components and degradation of the insulation materials. A low neutralization number is a sign that the oil remains pure and free from harmful acidic byproducts. Regular monitoring of the neutralization number is essential to ensure that the oil remains in good condition and continues to protect the transformer from internal damage.
Transformer Oil Uses:
Power Transformers:
Transformer oil is extensively used in power transformers across electrical distribution networks. These transformers handle high voltages and require excellent insulation and cooling to operate safely. The oil enhances the dielectric strength between windings and cools the transformer, ensuring efficient energy transmission from power plants to homes and businesses. Power transformers with oil insulation are found in substations, industrial plants, and renewable energy installations.
Distribution Transformers:
Smaller distribution transformers, commonly used for lowering voltage levels in local distribution networks, rely on transformer oil for insulation and heat dissipation. The oil prevents electrical arcing, maintains thermal stability, and helps extend the lifespan of these transformers, which are crucial in delivering electricity to homes, schools, and offices.
High Voltage Circuit Breakers:
Transformer oil is used in high voltage circuit breakers to quench arcs when the breaker interrupts a high-voltage electrical current. The oil’s excellent dielectric properties and arc suppression capabilities help extinguish arcs quickly, preventing damage to electrical systems and ensuring the safety and functionality of the circuit breaker.
Oil-Filled Switchgear:
In oil-filled switchgear, transformer oil acts as both an insulator and an arc extinguisher. The switchgear, used to control and protect power systems, often operates under high voltages. Transformer oil ensures that the switchgear components remain properly insulated while also dissipating the heat generated by electrical switching and arc formations.
Capacitors:
Some high-voltage capacitors utilize transformer oil to enhance dielectric performance and prevent internal discharges. The oil also absorbs heat generated within the capacitor, maintaining its thermal stability and extending the lifespan of the capacitor, especially in high-voltage applications.
Oil-Filled Voltage Regulators:
Oil-filled voltage regulators, used to stabilize voltage levels in power systems, also depend on transformer oil for insulation and cooling. The oil ensures that internal components, such as windings and contacts, are insulated from each other, preventing electrical breakdowns and enhancing the efficiency of voltage regulation.
Railway Traction Transformers:
In railway systems, traction transformers are used to supply power to trains, and transformer oil plays a vital role in insulating and cooling these transformers. The oil ensures that the transformers remain stable even under heavy load conditions, preventing breakdowns and ensuring safe and reliable rail operation.
Industrial Transformers:
Transformer oil is used in various types of industrial transformers, including furnace transformers, welding transformers, and rectifier transformers. These transformers are essential for heavy industries such as steel manufacturing, mining, and chemical processing. Transformer oil provides necessary cooling and insulation, ensuring that these transformers can operate under high-stress conditions without overheating or failing.
Instrument Transformers (CTs & PTs):
Current Transformers (CTs) and Potential Transformers (PTs), which are used to measure electrical currents and voltages in high-voltage systems, often rely on transformer oil for insulation and protection. The oil ensures the accuracy and safety of the measuring instruments, protecting them from electrical surges and heat.
Bushings and Insulation Systems:
Transformer oil is also used in bushings, which insulate electrical conductors passing through grounded barriers like transformer casings. The oil helps maintain the dielectric strength and thermal stability of the bushing, ensuring that electrical transmission remains safe and efficient, even at high voltages.
Oil-Filled Cables:
In some high-voltage oil-filled cable systems, transformer oil is used to prevent electrical discharge and ensure the smooth flow of electricity through the cables. The oil keeps the cable’s insulation system intact while acting as a coolant to prevent overheating in long-distance transmission lines.
Large Motors and Generators:
Transformer oil is sometimes used in the insulation and cooling of large electric motors and generators, particularly in industrial settings. The oil reduces the risk of electrical failure and overheating, improving the reliability and operational efficiency of these high-powered machines.
Oil-Insulated Reactors:
In electrical grids, oil-insulated reactors are used to control the flow of electrical currents and manage reactive power. These reactors rely on transformer oil for insulation and cooling, ensuring stable operation under varying load conditions.
Renewable Energy Systems:
Transformer oil is also essential in wind and solar power systems, where transformers are used to step up or step down voltages. These renewable energy transformers use oil for both cooling and insulation, ensuring they operate efficiently even in remote locations with high exposure to environmental stresses like temperature fluctuations.
Frequently Asked Questions
-
What are the primary applications of AQUAL TO16?
AQUAL TO16 is mainly used in electrical systems such as power transformers, distribution transformers, high-voltage switchgear, and oil-filled circuit breakers. Its excellent dielectric properties and heat transfer capabilities make it suitable for a wide range of high-voltage insulation and cooling applications.
-
-
-
What are the benefits of using AQUAL TO16 in high-voltage equipment?
AQUAL TO16 provides superior insulation and cooling, reducing the risk of electrical breakdowns and overheating. Its ability to withstand normal oxidation ensures long-term stability and minimal maintenance, extending the life of electrical equipment and reducing operational costs.
-
-
-
How does AQUAL TO16 perform under varying temperature conditions?
AQUAL TO16 is formulated to maintain its insulating and thermal properties across a wide range of temperatures. It has a low pour point, making it effective in cold climates, and a high flash point, which enhances safety in high-temperature environments, ensuring reliable performance even in extreme conditions.
-
-
-
Can AQUAL TO16 be used in older transformers or is it only for new installations?
AQUAL TO16 is compatible with both new and existing transformers. It can be used for topping up older transformers, provided that a proper compatibility test is conducted. M The transformer oil properties make it an excellent choice for extending the operational life of aging equipment.
-
-
What is the typical service life of AQUAL TO16, and how can it be maintained?
The service life of AQUAL TO16 can vary depending on operating conditions, but it generally provides long-term performance with minimal degradation. Regular testing for dielectric strength, moisture content, and acidity can help maintain its properties. In case of significant degradation, reconditioning or replacement may be required to ensure optimal performance.